Building a deck is an exciting venture that opens up a world of possibilities for creating the perfect outdoor oasis. However, a sturdy and reliable deck requires a solid foundation, and that’s where deck framing comes into play.
In this guide, we’ll take you through each step of the deck framing process, from understanding the essential components to selecting the right materials and mastering proper techniques.
Whether you’re a seasoned DIY enthusiast or a first-time deck builder, our easy-to-follow instructions and expert tips will equip you with the knowledge to construct a deck that stands the test of time.
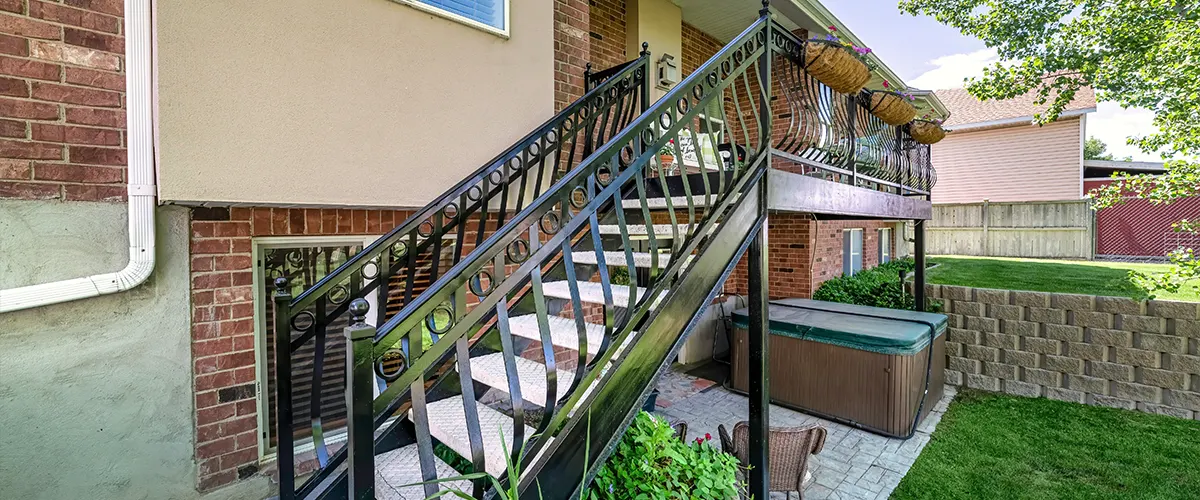
What Is Deck Framing
Deck framing refers to constructing and assembling the structural framework that supports a deck’s surface or decking boards.
It involves arranging various components, such as deck joists, rim joists, support posts, beams, and ledger boards, to create a stable and sturdy foundation for the deck.
Deck framing is a critical step in the deck building process, as it provides the structural integrity and support necessary to ensure the safety and longevity of the deck. Properly constructed deck framing is essential for creating a solid and reliable outdoor space that can withstand various weather conditions and loads.
This includes the posts, beams, and rim joist that will hold up the decking surface. Deck framing can be done with either wood or metal framing members. The frame is where the deck boards are installed, and it’s attached to the house with a ledger board.
- Wood is the most common material for deck framing, but metal can be used as well. The most important thing to consider when choosing materials for your deck framing is the weight of the decking material you will be using.
- Metal framing is much stronger than wood, so it can support more weight. However, metal is also more expensive and may not be as aesthetically pleasing as wood.
Benefits of Solid Deck Framing
- Enhanced Structural Integrity
- Longevity and Durability
- Supports Custom Deck Designs
- Suitable for Various Decking Materials
- Increased Safety
A solidly framed deck ensures the safety of everyone who uses it. It minimizes the risk of sagging, warping, or shifting, which can lead to accidents or injuries. By adhering to building codes and industry standards during the framing process, you create a secure and hazard-free outdoor space.
- Ease of Maintenance
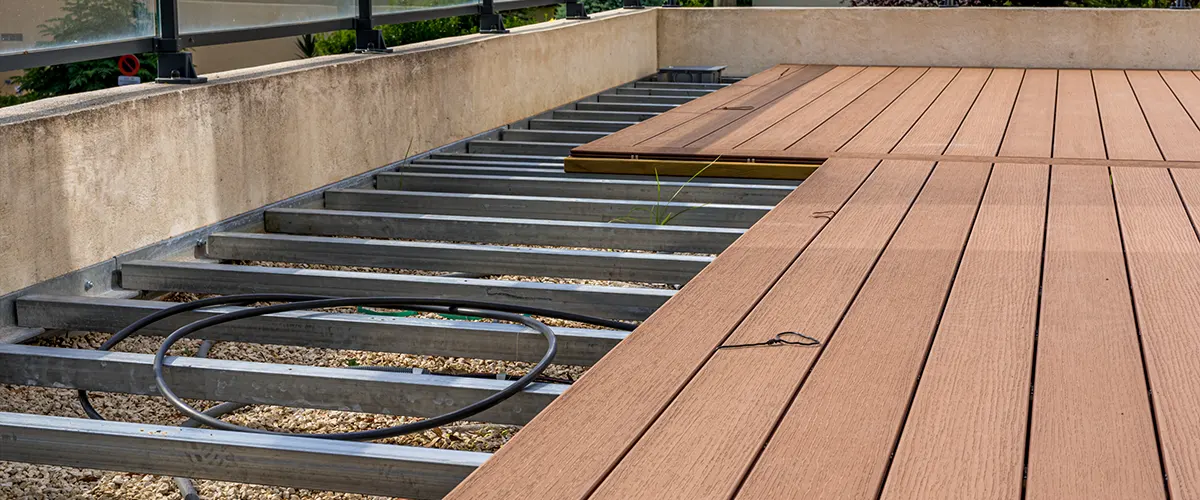
How To Frame A Deck
- Planning and Preparation: Before you begin, familiarize yourself with your deck plan and local building codes. Prepare the required materials for framing, including lumber, wood, construction screws, and lag screws. Ensure you have the right tools for accurate measurements and alignments, such as a level, tape measure, and framing square.
- Establishing the Ledger Board: To begin framing, attach the ledger board to the side of your house. It acts as the starting point for your deck, supporting one side of the structure. Use lag bolts to secure the ledger board, ensuring it offers additional support with structural screws.
- Installing Support Posts: Measure and mark the positions for the support posts on your deck plan. Dig concrete footings at each marked location, considering soil conditions and local building requirements. Place support posts in the concrete footings and use lag screws to anchor them securely.
- Determining Joist Size and Spacing: Select the appropriate joist size based on the tributary area it will support. Joists are horizontal framing members that run perpendicular to the ledger board, providing the deck's primary support. Refer to building codes to determine the correct spacing between joists, usually 16 inches.
- Placing Rim Joists and Outer Joists: Frame the outer edge of the deck with rim joists, securing them to the ledger board and support posts using joist hangers. Place the outer joists in the same direction as the rim joists and secure them with construction screws for a sturdy frame.
- Adding Beams and Diagonal Bracing: Install beams along the centerline of the deck, supported by the outer joists and connected with construction screws. Add diagonal bracing between beams and support posts to prevent racking and add stability.
- Ensuring Levelness and Squareness: Check that your deck frame is level and square throughout the construction process. Use a level and framing square to make adjustments as needed, ensuring a precise and balanced structure.
- Decking Installation: You can install the deck boards once your deck frame is complete. Lay the decking boards across the joists, leaving equal spacing between them for proper drainage. Use deck screws to attach the boards securely.
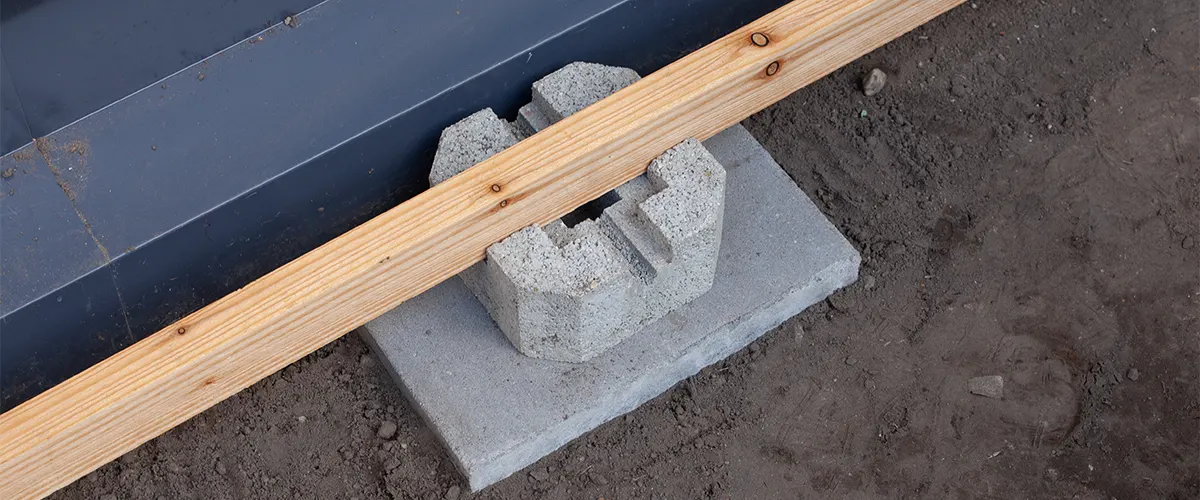
Best Materials For Different Deck Framing Parts
- Deck Joists: Pressure-treated lumber is an excellent choice for deck joists, offering both affordability and durability. These sturdy boards provide a solid framework for the deck surface and can withstand various weather conditions.
- Rim Joist: Just like deck joists, pressure-treated lumber is the ideal material for rim joists. As a critical component of the deck's perimeter, the rim joist ensures stability and support for the entire structure.
- Deck Surface: For the deck surface itself, consider using composite decking. Composite decking is a popular choice due to its low maintenance requirements, resistance to rot, and longevity. It provides a smooth and attractive surface for your outdoor living space.
- Ground-Level Decks: When building a ground-level deck, consider using concrete footings or deck blocks to elevate the frame off the ground. This approach helps prevent direct contact with soil, reducing the risk of moisture-related issues and ensuring better longevity for the deck.
- Stationary Surface: If your deck is a stationary surface, meaning it won't be moved or adjusted regularly, pressure-treated lumber for the frame is a cost-effective and reliable option. It provides the necessary strength and support for a stationary deck.
- Deck Design: The materials you choose for deck framing will largely depend on your deck design and intended use. Pressure-treated lumber is versatile and commonly used for most deck designs, providing a solid foundation for various configurations.
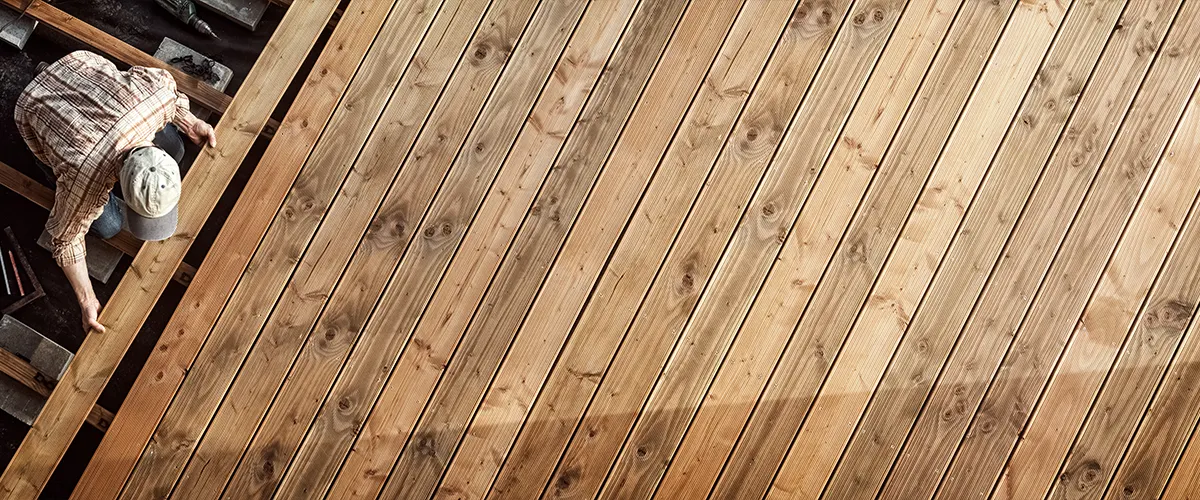
Deck Framing FAQs
The choice between 2×6 and 2×8 deck joists depends on the specific requirements of your deck. 2×6 joists are generally suitable for most decks with standard loads and spans. They are a cost-effective option and work well for small to medium-sized decks.
However, if your deck will carry heavier loads or require longer spans, 2×8 joists may be a better choice. The larger size provides increased strength and stability, accommodating greater weight and longer distances between support points.
The spacing for deck framing, particularly for joists, depends on various factors such as the decking material, load requirements, and local building codes.
As a general guideline, standard wood decking typically requires joists to be spaced at 16 inches on center for optimal support and stability. However, different decking materials may have specific spacing requirements, so it’s essential to refer to the manufacturer’s recommendations.
For heavy loads or special conditions, closer joist spacing may be necessary. Always adhere to local building codes to ensure compliance with safety standards in your area.
Let The Experts Deal With Deck Framing
Building the framing for your deck is a crucial step that requires precision, knowledge, and experience. We encourage you to leave this task to our skilled professionals to ensure a sturdy and long-lasting foundation for your dream deck.
Our team has extensive experience in deck framing, using the right materials, and adhering to local building codes to create a structure that stands the test of time.
Save yourself the hassle and potential pitfalls of DIY framing, and let us bring your vision to life with our top-notch craftsmanship. Contact us today at (865) 801-4545 to discuss your deck installation needs and embark on an exciting journey to transform your outdoor space into a breathtaking retreat.